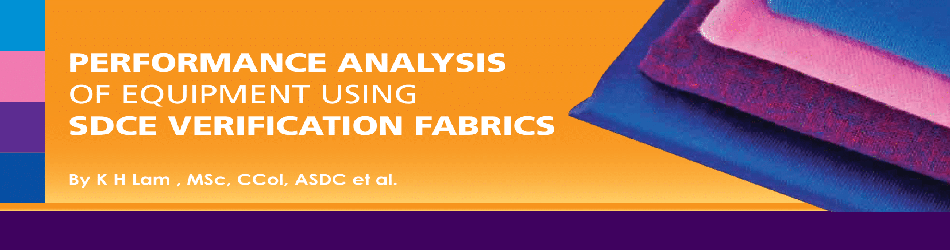
ABSTRACT
Instruments are calibrated, and then reliable test results will be obtained ? Are there simple and effective tools to keep test instruments well performed, especially for physical test? (e.g. ICI pilling, Martindale, random pilling and tensile...) Moreover, many factors affect the performance of tests. Therefore, working with SDC Enterprises (SDC) and all the leading independent textile/softlines testing labs, KMS adopts SDC Verification Fabrics, as the reference, to effectively monitor test, well as a whole. In so doing, if different test instruments pass through the verification regularly, even though they are operated in different situations (e.g. by different lab technicians...), reliable test results can be obtained.
INTRODUCTION
Organisations involved in textile testing show great concern with regards to the reliability, precision and accuracy of their laboratory equipment. Equipment used in the physical test area, for determining important properties such as tensile, bursting, tearing strengths, resistance to abrasion and propensity to pilling, are heavily reliant on external service and calibration. Invariably this facility is provided by engineers of the machinery manufacturer, performed by trained professional mechanics, using specialised tools and test materials.
In general, force or pressure, speed, distance, current or voltage, energy etc. are the calibration criteria of physical testing machines. This approach is perceived to leave shortcomings, gaps and voids:
1) Only trained professionals can check and calibrate the machines; needless to say, this can be a costly exercise.
2) Servicing and calibration may only take place quarterly or even annually in some occasions. Changes in the working environment and/or equipment between these calibration intervals may be hard to detect, and subsequently influence the reliability of the test data.
3) From the standpoint of the physical testing laboratory,
use for the calibration of a machine's performance, the actual test results generatede are the ultimate goal.
There are few specific international standards, which call for the use of reference materials to be used in conjunction with /or materials, e.g. Multi-fibre fabric and blue wool standards.However, many international standards, in particular " physical" test method it methods do not include the use of a the standard refference material to verify the condition of the apparatus being used ,and therefore validity of the result obtained
SDC Enterprises have combined their extensive knowledge of fabric quality control, textile testing, dyeing and continuity of technical performance in test materials to develop a range of verification fabrics to improve the controls available to organisations involved in textile testing. Use of these fabrics will provide a simple and effective way to implement verification or control procedures for their testing.
METHOD
The purpose of this study was to explore the use of SDCE's Verification Fabrics in the performance analysis of laboratory equipment. This study focuses on SDCE Verification Fabric #2955 and #2960, the chosen International Standard, and utilises six physical testing machines. This study was conducted at intervals throughout the day/week, using a diverse operating team, bringing an element of subjectivity to the exercise.
PRINCIPLES
(A) Consistent textile materials to be used for the performance analysis:-
1) Woven, Plain-Weave, Product code 2955 Verification Fabric PH 2) Knitted, Product code 2960 Verification Fabric PI
(B) Test equipment designated for the exercise:-
1) Tensile strength tester, code UST
2) Martindale abrasion and pilling tester, code MTD
3) Bursting strength tester, code BTA
4) Electronic tearing tester, code ELT
5) Random tumble pilling tester, code RPT
6) ICI pilling tester, code ICI
(C) The test pieces will be subjected to the following International Standard Test Methods:
1) Determination of Maximum Force using the Grab Method: ISO 13934-2
2) (a) Abrasion Resistance of Textile Fabrics: ASTM D4966, Option 3 (% mass loss)
(b) Determination of Fabric Propensity to Surface Fuzzing and to Pilling: ISO 12945-2
3) Hydraulic Bursting Strength of Textile Fabrics: ASTM D3786
4) Tearing Strength of Fabrics by Falling-Pendulum Type (Elmendorf): ASTM D1424
5) Determination of Fabric Propensity to Surface Fuzzing and to Pilling: ASTM D3512
6) Determination of Fabric Propensity to Surface Fuzzing and to Pilling: ISO 12945-1